Achieving Supply Chain Assurance Using Time-Tested Mitigation Strategies
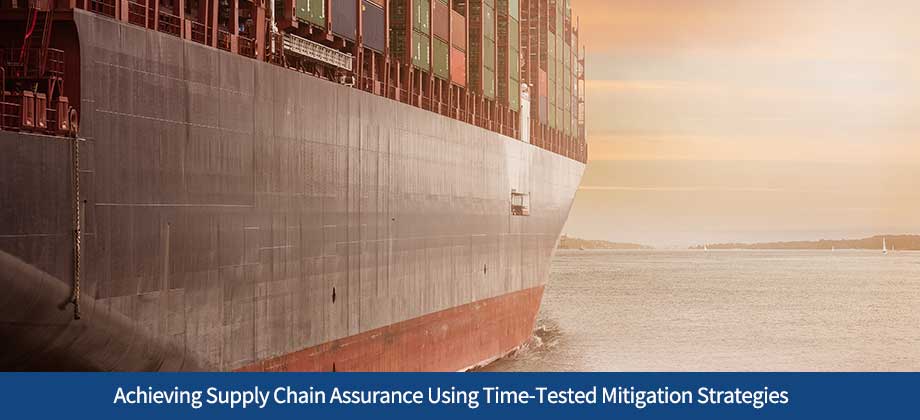
In the wake of persistent supply chain disruptions, manufacturers are turning to time-tested mitigation strategies with enhanced tactics to achieve greater supply assurance in 2023. As surveyed manufacturing executives have reported, 72% believe that critical materials shortage and ongoing supply chain issues remain the biggest uncertainty for their industry. To mitigate these risks, manufacturers are increasingly utilizing digital technology while also adopting traditional methods such as local capacity building and just-in-time sourcing with redundancy in mind. By doing so, they hope to gain a more secure and reliable network of suppliers.
The Risks Associated with Supply Chain Disruptions
The recent pandemic has highlighted the importance of supply chain assurance and the risks associated with disruptions. As manufacturers have come to realize, lack of critical materials or a sudden breakdown in their supply networks can lead to significant losses in terms of cost, time, and reputation. Even a slight disruption can have a major impact on manufacturers. These disruptions can result in significant financial losses, in addition to delays and reputational damage if not properly addressed.
The current supply chain landscape presents numerous challenges for manufacturers, most notably the rising prevalence of critical materials shortages. These shortages are due to a combination of factors, such as increased global demand, disruptions in transportation and logistics, and the limited availability of raw materials. As such, manufacturers must be proactive in their approach to mitigating supply chain risks and addressing these shortages. This includes implementing strategies to diversify sourcing and increase visibility in their supply chains. Additionally, they must take actions to reduce costs associated with procurement and ensure that they have sufficient stock levels of necessary items on hand. By taking such steps proactively, manufacturers can better protect themselves from unexpected disruptions or delays in production due to critical materials shortage.
It is therefore essential for manufacturers to adopt both digital technologies and traditional strategies such as local capacity building and just-in-time sourcing with redundancy in mind. This will help ensure that their networks are resilient enough to handle sudden changes in demand or unplanned events that may arise due to the disruption of global supply chains. Doing so will also enable them to identify potential sources of materials or services quickly, which will help them stay agile and competitive in the long run.
In addition, manufacturers must also utilize digital technology for improved risk management. With the help of robust systems that can track suppliers, anticipate disruptions, and identify alternatives quickly, businesses will be better equipped to manage their networks more effectively during periods of disruption. By leveraging advanced analytics and machine learning algorithms, companies can gain valuable insight into their operations and spot potential risks ahead of time. This will enable them to take necessary measures promptly and reduce the likelihood of supply chain disruptions, thereby increasing their operational efficiency and protecting their reputation in the marketplace.
Traditional Mitigation Strategies to Increase Supply Assurance
Traditional mitigation strategies such as building local capacity and diversifying sources of supply can help to ensure supply assurance. This approach helps to reduce exposure to risks associated with a single source and increases the availability of goods in case of any unforeseen disruptions. By maintaining redundant sources of supplies, manufacturers can have the flexibility to switch suppliers when needed without compromising on quality or quantity.
Additionally, setting up manufacturing units closer to the end customer ensures quicker delivery times and better control over the production process. Such an approach also allows businesses to monitor their supply chain more closely, ensuring compliance with regulations and standards while minimizing costs associated with long-distance shipments. Ultimately, these strategies help manufacturers minimize potential risks while ensuring timely delivery of goods.
Automation solutions are being used as well, which provides real-time data on inventory levels and supplier performance. Such solutions can help manufacturers keep an eye on their suppliers more closely and spot any irregularities or bottlenecks that could potentially lead to delays in production. Moreover, such automation solutions can be integrated with SRM platforms to provide an even more comprehensive view of the entire supply chain process.
By utilizing these approaches, companies can not only ensure supply assurance but also remain competitive in a highly taking a proactive approach, businesses can ensure that their supply chains remain resilient and competitive while minimizing potential risks associated with the industry. This enables manufacturers to optimize production processes and guarantee timely delivery without compromising on quality or quantity. This way, manufacturers are better able to guarantee supply assurance even in the face of unexpected disruptions.
Utilizing Digital Technology for Improved Risk Management
Utilizing digital technology for improved risk management is becoming increasingly essential in the manufacturing industry. Advanced analytics and machine learning can help businesses gain valuable insights into their supply chain system, allowing them to identify potential risks and find solutions to address them before they become a problem. This enables manufacturers to be proactive in managing their supply chain disruption risks rather than reactive. Additionally, digital technology can also help optimize production process and guarantee timely delivery without compromising on quality or quantity. By leveraging both traditional mitigation strategies and innovative tactics enabled by digital technology, companies can ensure reliable production processes with greater efficiency and reduce the financial losses associated with supply chain disruptions.
By leveraging digital technologies such as advanced analytics, automation, and SRM platforms, manufacturers can gain better visibility into their supply chains and be better prepared to respond to potential risks and disruptions. Digital technologies allow manufacturers to gain a deeper understanding of their supply chain processes so they can identify irregularities or bottlenecks before they become an issue and take preemptive action. Automation also makes it easier for manufacturers to track inventory levels in real-time and make sure they have all the components required for production at any given moment. Finally, digital technologies are also enabling manufacturers to set up redundancy sources such as dual or multiple suppliers who have the same capability as the primary supplier for added insurance against unexpected disruptions or issues.
Building Local Capacity for Reliable Supply Chains
Building local capacity for reliable supply chains is key to mitigating the risks of supply chain disruptions. By cultivating a localized supply base, manufacturers are able to reduce their reliance on global suppliers and increase redundancy in their operations. This reduces the financial losses caused by delays or shortages of critical materials, resulting in improved production processes with greater efficiency. Additionally, investing in local capacity can help companies take advantage of opportunities such as preferential tariffs and reduced transportation costs. Furthermore, businesses are better able to respond to changing customer demands and maintain quality standards while keeping costs low. With a more secure and resilient supply chain, manufacturers can ensure their operations remain safe and reliable.
Building local capacity for reliable supply chains can involve many different approaches. Companies can invest in better inventory management systems to ensure they have the right materials on hand when needed. They can also consider diversifying their supplier base, reducing their reliance on a single source and building relationships with suppliers closer to home to reduce transportation costs. Additionally, businesses should take proactive measures to identify potential supply chain risks and develop mitigation strategies accordingly. For instance, organizations could consider revising their production schedules or engaging in strategic stockpiling of materials before disruptions arise. With these measures combined, companies can create a secure and robust supply chain that reflects current market demands and serves as an insurance against future uncertainties.
Moving from Just-in-Time Sourcing to Create Redundancy
Creating redundancy in the supply chain is a cost-effective and long-term solution for manufacturers facing disruption to their supply chains. By investing in multiple sources of materials, companies can ensure faster response times due to fewer material shortages and reduce their reliance on one supplier. Companies can also take advantage of economies of scale by aggregating their demand and negotiating better terms with suppliers. Additionally, improved production processes such as adaptive planning systems make it easier to manage inventory levels and respond quickly to changing customer demands. Furthermore, strategic stockpiling allows companies to maintain an adequate supply of materials while avoiding the need for costly quick purchases due to shortages or delays. All in all, moving from just-in-time sourcing to create redundancy is an effective mitigation strategy for manufacturers that can help them protect against uncertain market conditions while keeping their operations safe and reliable.
In conclusion, manufacturers must embrace digital technology while leveraging traditional strategies to ensure that their supply chains remain resilient enough to handle unexpected events. By doing so, they can build greater confidence among customers and stakeholders towards their operations while mitigating risk and maintaining competitive advantage. By taking such a proactive approach, companies can protect against costly supply chain delays or interruptions that may result in financial losses.
Your privacy is important to us. ARF Financial will never sell or rent your information to any third party. Click here for more information about our privacy policy.